asicdesign
Are you interested in your own chip?
With your own chip - an ASIC (Application Specific Integrated Circuit) - you can now make yourself independent of supply bottlenecks and know-how theft. As a renowned German chip manufacturer, we develop, produce and deliver your customised ASIC free of charge.
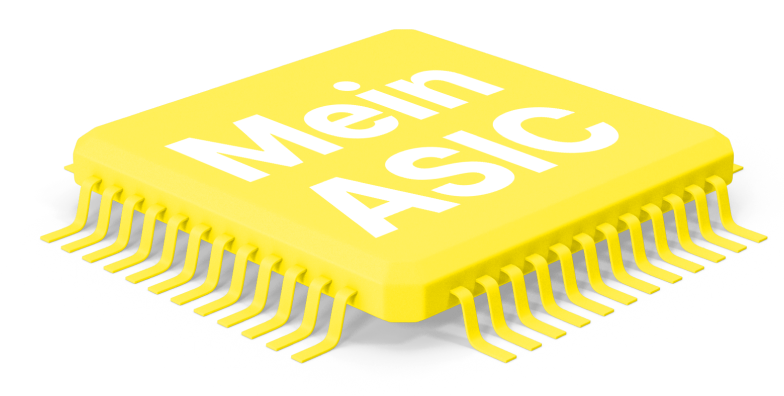
why asic development
Will an ASIC solve my problems?

Delivery and planning security
As a buyer of small or medium quantities, I am not served directly by the semiconductor manufacturer but via distributors. The semiconductor market is very cyclical and in times of component shortages, I cannot count on preferential supply and run the risk of having to reduce my production and not being able to serve my customers.

Announcements
I constantly have problems with component discontinuations, which cause high redesign costs and my products have to be constantly re-qualified and re-certified. Maintaining my products requires a lot of resources that I cannot allocate to important innovations. Last-buy storage costs tie up capital, which has a negative impact on my balance sheet.

Competitive system costs
Particularly in the wake of globalisation, I am looking for ways to reduce my unit costs in order to be attractive and competitive for my customers. Indirect costs that are too high - due to the large number of components, storage and assembly costs, etc. - are a burden on my margins and need to be optimised.

Space requirement
The form factor of my current system solution no longer meets the requirements of my customers and makes my product appear ‘old-fashioned’.

System performance
My current system solution has performance problems and I am struggling with high latencies. The energy consumption of my solution no longer meets the future low power requirements of my customers - I have a battery-operated system that needs to be optimised in terms of power consumption.

Protection of know-how
A significant part of my unique selling point lies in the electronics, which are exposed to a high risk of re-engineering and copying due to the current design, making it easy for competitors to take over my expertise.
That's why my own chip is superior
With my own chip, I have full control and independence. I can integrate my individual functions in the smallest form factor, at low cost and better protect my expertise.
Chip off the shelf
Features
- I pay for many functions that I don't need with
- High energy consumption
- No one-off development costs
- Allocation problems with high demand
- High proportion of external components
- No technical differentiation, many competitors use the same chip
Own chip

Features
- Cost optimisation - I only pay for the functions I need
- Energy consumption can be adapted to my requirements
- One-off development costs that are amortised through production
- The chip is only delivered to me
- External components can also be integrated
- Differentiation and know-how protection
4 phases to your own chip
How do I implement my ASIC project? The realisation of an ASIC project is a very complex undertaking and requires a great deal of expertise and experience. It involves several trades that are contributed by differently specialised partners - the collaboration between these partners must also be well coordinated and managed. Ideally, an ASIC design house not only takes on the development of an ASIC, but also acts as a one-stop-shop partner for the holistic realisation of the ASIC project through to the supply chain. The realisation of an ASIC project can take place in the following phases:
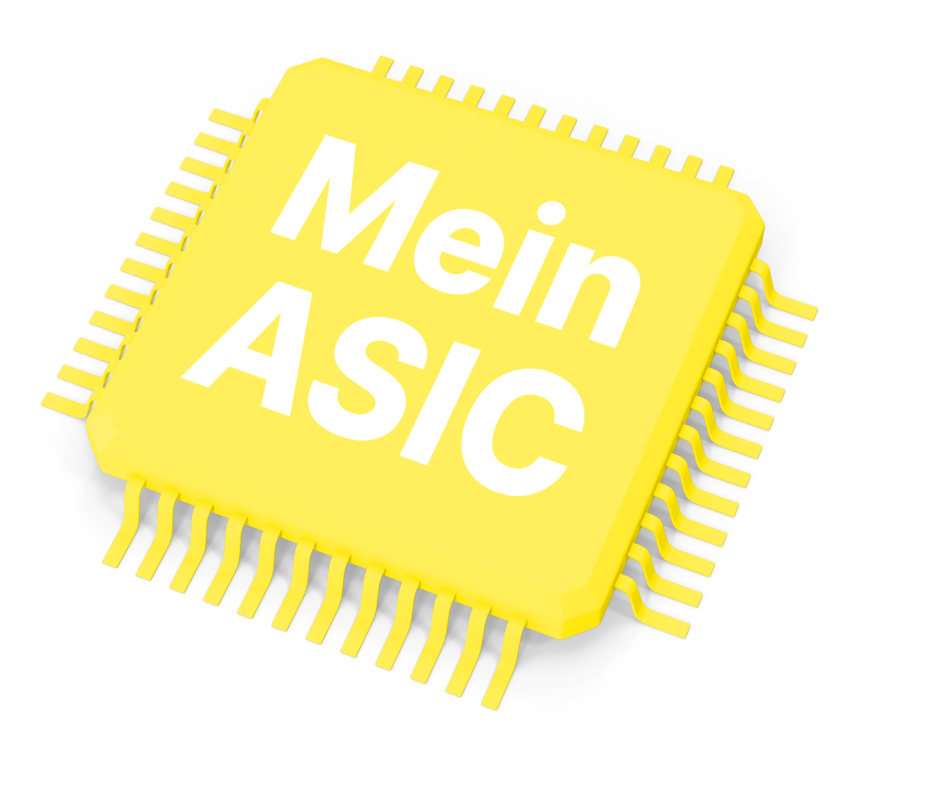
Phase 1 | Machbarkeitsstudie
Feasibility study
In order to assess whether an ASIC is the right approach, the strategic, technical and economic requirements must first be defined and analysed.
Strategic requirements
- Expertise protection
- Independence from suppliers
- Delivery reliability
Technical requirements
- Which analogue and digital circuit components should be integrated?
- What system performance is required?
- Which functions are implemented in hardware and which in software?
Phase 2 | System Design
Phase 3 | Design realisation
Phase 4 | Industrialisation
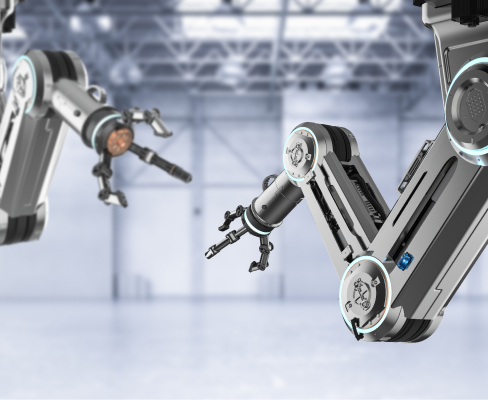
A product manufacturer from the automation industry had the following problems:
His expertise was implemented to an essential extent in his electronics and this was implemented with standard components on a printed circuit board. As the manufacturer was not supported directly by the semiconductor manufacturers due to a lack of quantities, it repeatedly had to contend with massive supply bottlenecks during the cyclically recurring semiconductor shortages.
In the post-corona period, only 30% of its required components were delivered in some cases - which caused existential problems due to a massive slump in sales and longstanding customers switched to alternative components from competitors.
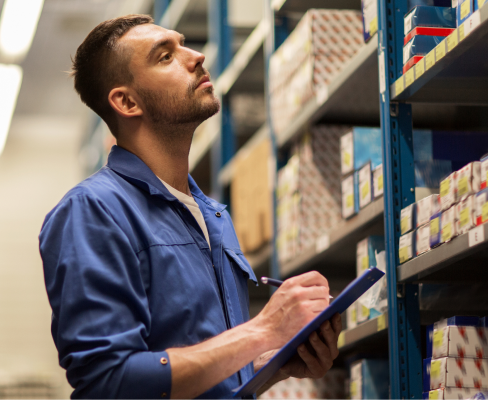
A product manufacturer from the automation industry had the following problems:
Furthermore, his products were used in safety-relevant applications, which not only led to high buffer stock and redesign costs due to the large number of components in the event of discontinuation, but also repeatedly resulted in high costs for recertification.
Due to the implementation with standard components, his expertise was increasingly copied by competitors from low-wage countries and his market was flooded with comparable, cheaper products.
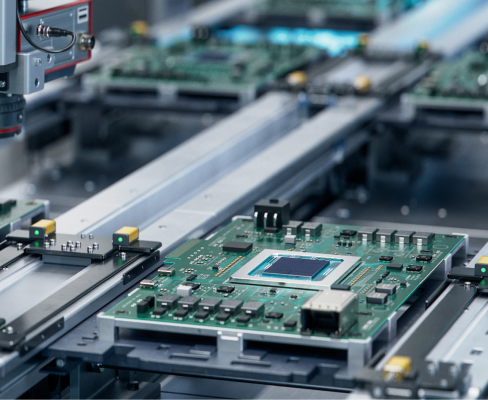
New ways
In the course of a new development, the product manufacturer was interested in an ASIC solution to minimise the problems mentioned. However, the low quantity projection meant that no semiconductor manufacturer was interested. As it was a mixed-signal application with a radio interface, it was also not easy to find the necessary development expertise, particularly in the areas of analogue and RF.
Ultimately, an ASIC design house specialising in industrial applications was identified and selected as the general contractor. As part of a feasibility study, the requirements of the desired ASIC were jointly specified and the architecture designed.
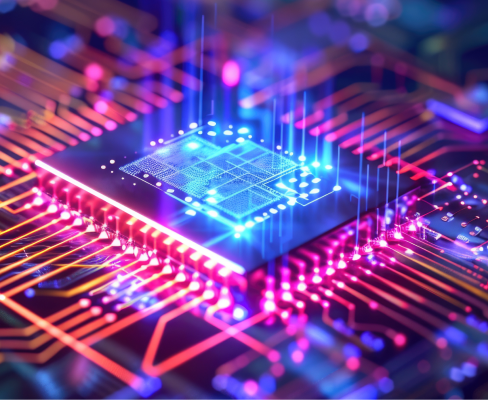
Your own chip
Thanks to the ASIC Design House's good contacts, the ideal process technologies for this application and corresponding manufacturing partners - even for smaller quantities - were identified. As part of the feasibility study, the development costs and unit costs were also calculated and project plans drawn up. More than 100 discrete components of the previous implementation were implemented in the ASIC in combination with new features such as a new innovative fieldbus interface in conjunction with a cryptocore to increase data transfer security.
Compared to the conventional solution, the ASIC reduced BOM costs by 75%. The development costs of the ASIC were amortised within 3 years.
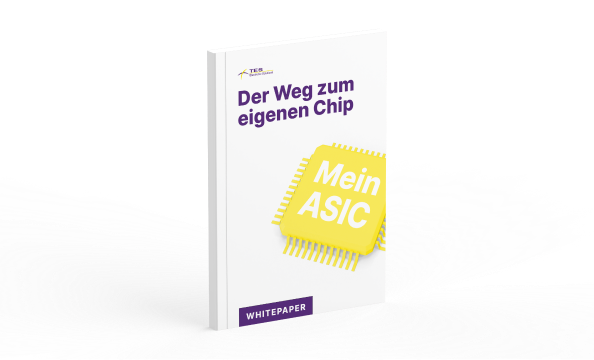
Whitepaper
The journey from the initial idea to your own ACID. Challenges and opportunities, backed up with facts and figures.
Wiki
Terms that are important in chip development, briefly explained.
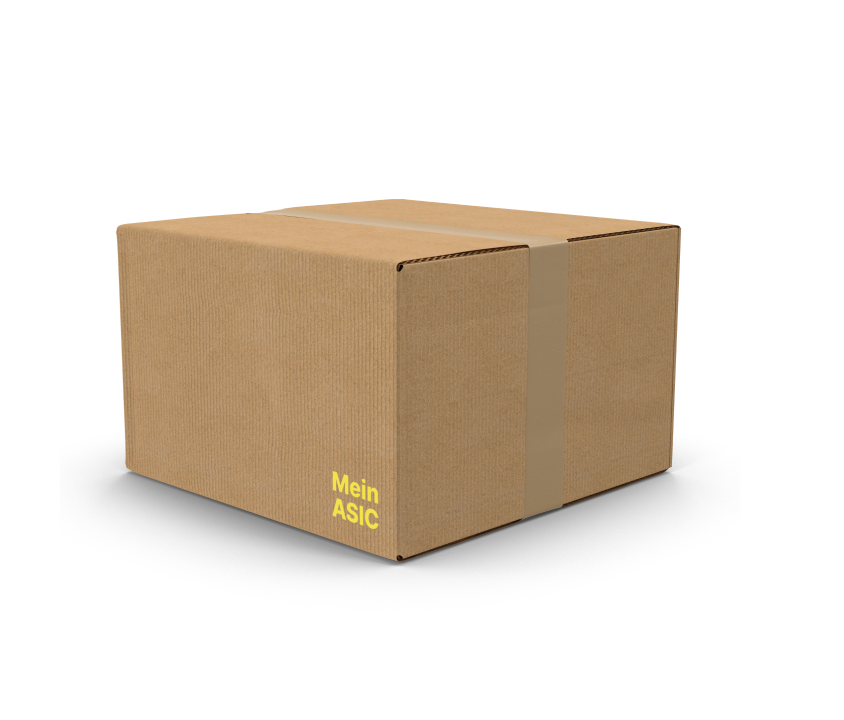
ASICs - also for industrial customers with smaller quantities
Auch für Industrieunternehmen mit geringeren Stückzahlen können individuelle ASIC-Lösungen realisiert werden. Wenn renommierte Halbleiterhersteller aufgrund unzureichender Stückzahlen oder mangels Entwicklungsressourcen kein Interesse an ASIC-Lösungen zeigen, können spezialisierte ASIC Design House Partner der Weg zum Ziel sein.
Im Zuge von – der Entwicklung vorgeschalteten – Feasibility Studien, erarbeiten ASIC Design Häuser, zu überschaubaren Kosten, alle Voraussetzungen und Konditionen für ein ASIC Projekt und liefern damit eine fundierte Grundlage für eine rationale Entscheidung, ob eine ASIC Lösung für ein Unternehmen sinnvoll ist.
Do you have any questions?
What costs will I have to expect? How long can such a process from the idea to my own ASIC take in my case? In order to be able to answer these questions at least roughly, we would like some information from you and would be pleased to hear from you!